As many of you know I have a passion for paper that comes from a long history of making art, especially since I have been printmaking in recent years. I have dabbled in making handmade paper, and am always interested in learning more.
Recently I had the extreme fortune to be able to take a look behind the scenes at the Schut papermill in the Netherlands. The Schut papermill, part of the Clairefontaine group, is a relatively small mill which allows them to make bespoke batches of paper upwards from 2 tonnes.
Part of their production is distributed through Clairefontaine, and I noticed the mill especially through their excellent Simili Japon paper, which is usually sold for calligraphy but is also very suitable for printmaking - even when using the rather demanding japanese woodblock printmaking technique, the paper has managed prints of over 20 impressions with no issues.
The other super interesting part of Schut’s activities are their contributions to sustainability by supporting circular economy - meaning for example, they make paper that has 50% tomato leaf fiber in it (unused waste from the tomato growing industry), and 20% tulip bulb fibers (from the Dutch bulb growing industry). Now tomatoes grown can be sold in cardboard boxes that are made from the plant material that otherwise would be thrown away.
It was a very interesting visit where Paul Spies, key account manager and business developer for Schut, explained the various activities of the mill, and took me on a tour around the facilities.
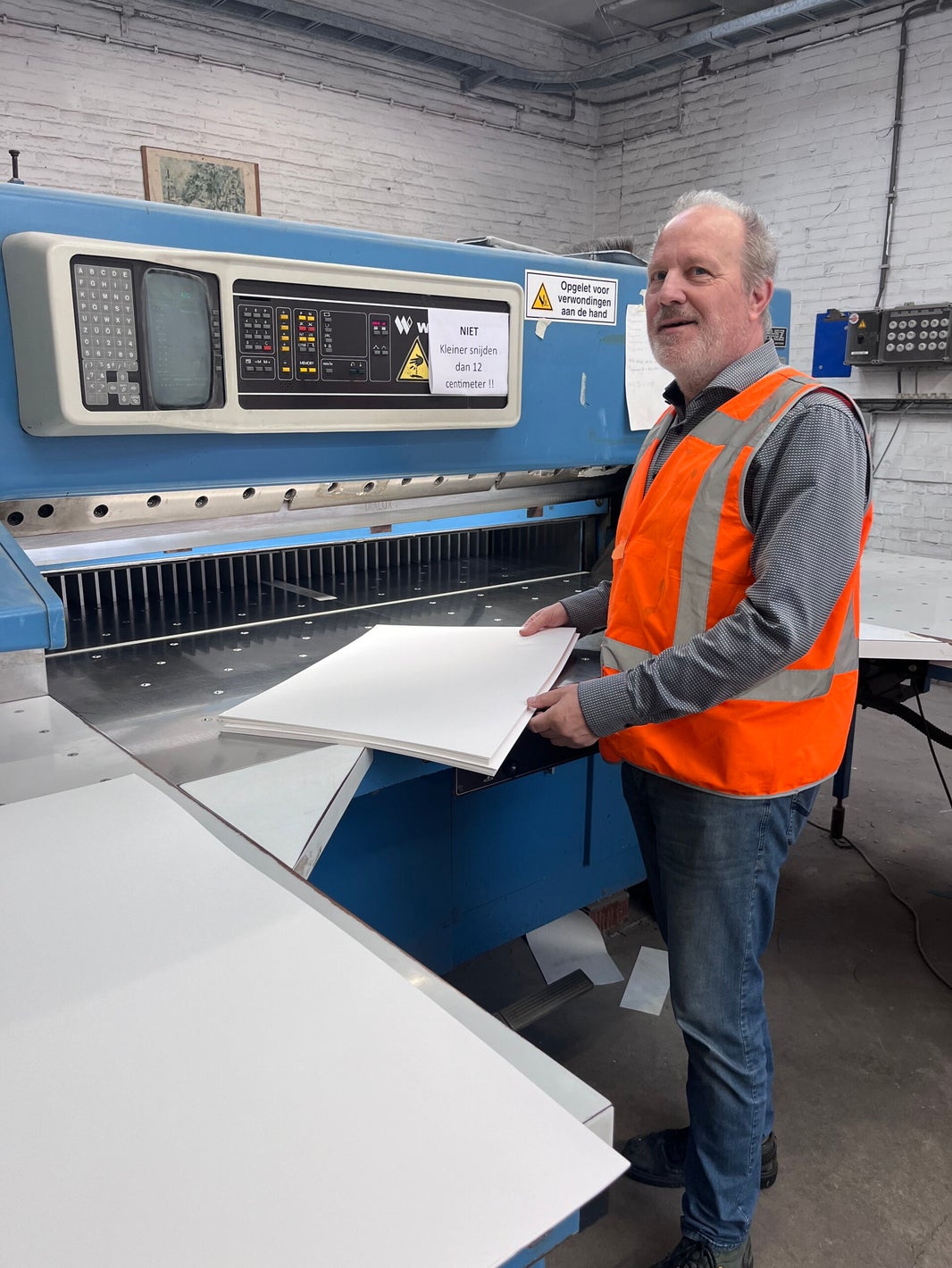
Paul described to me how the Schut papermill can produce bespoke paper upwards from 2 tonnes, and (after testing) can include fiber from other producer’s production waste (such as spent tomato plants, and also grass). Walking by huge bags of ready-to-use grass fiber, we entered the hall that houses the start of the production line.
Huge packs of pre-processed fiber (around 1’200 kg, image on the left) are fed by conveyor belt into a huge vat containing 16’000 liter water, which you can see on the right. The maximum fiber length is 1.2mm. Interestingly, the ready-to-use fiber sheets looked just like what I privately buy to make my paper with!
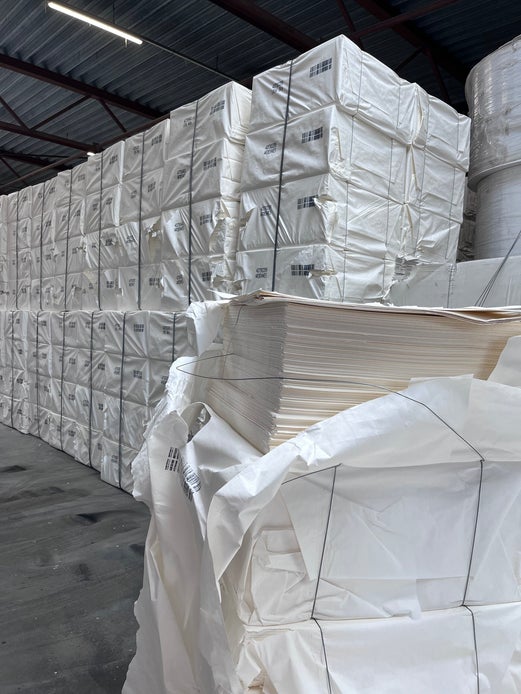
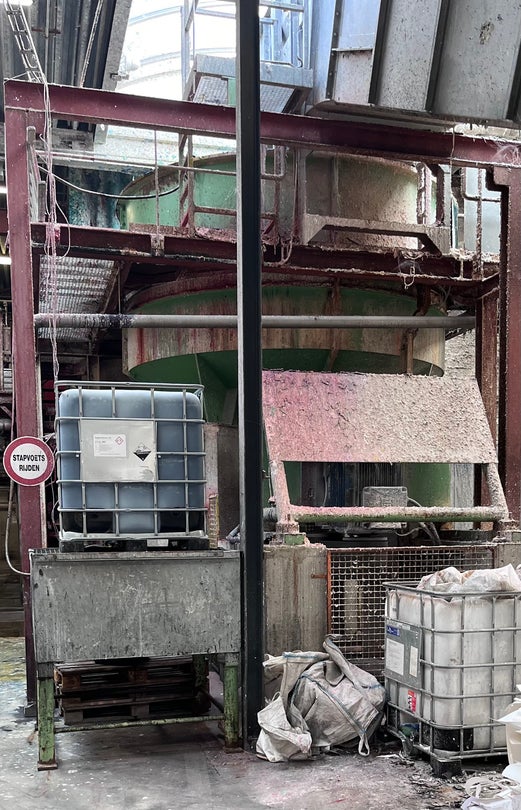
Here you can see the pulp being ground (left), and after moving it to several other vats (right), it gets colour added if needed, and made thinner and thinner until it's super smooth and ready to be fed into the paper machine. Below left a look into an empty vat.
Paul also showed me the rolls and felts they use (a little larger than mine!) to create different paper textures.
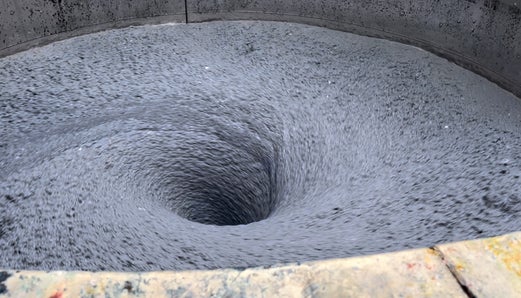
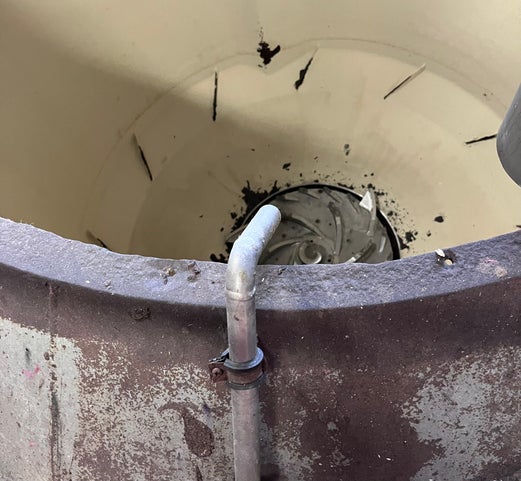
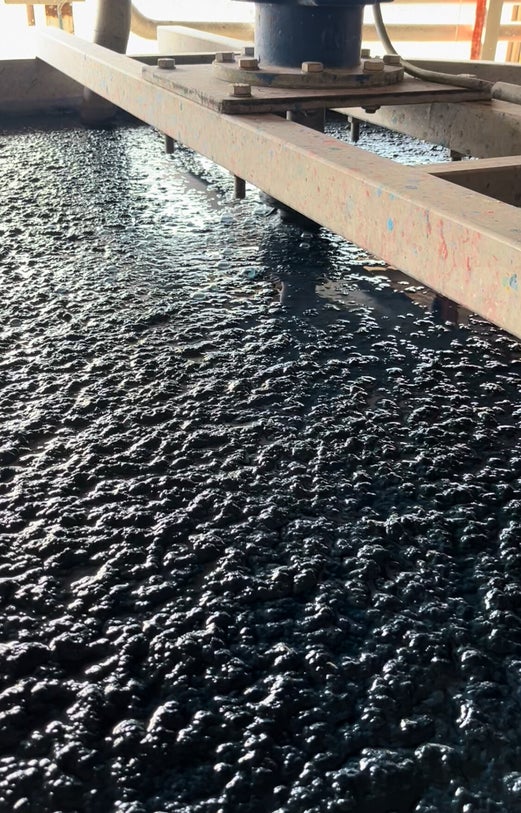
And then, paper is made. The intricacies of the machine are too many to cover in this post, but basically the slurry is cast as paper and then water is gradually removed until it's dry enough to size - which happens with potato starch, after which the paper is dried again, calendared if needed (smoothened between hot rollers), and rolled onto a massive roll which can be exchanged for an empty one whilst the machine is running. When we were there, there was already some 5600m or paper on the roll!
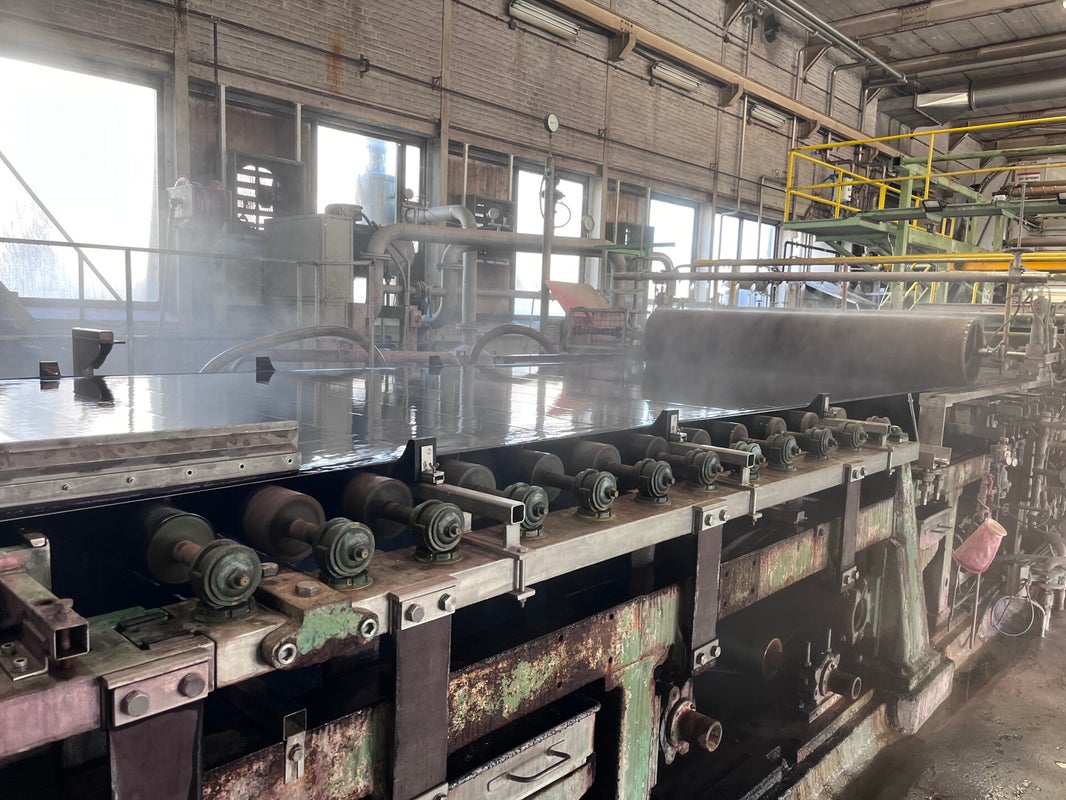
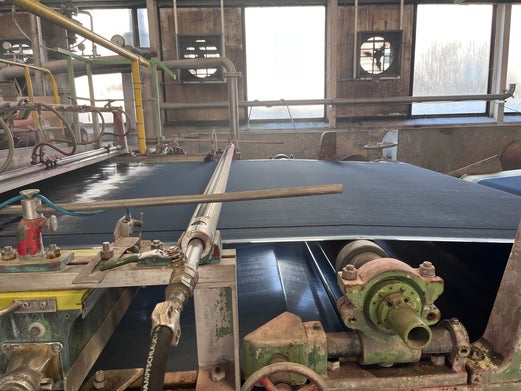
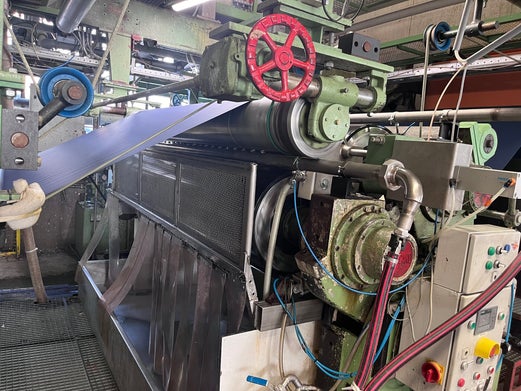
After this, the paper can be shipped as roll, or cut smaller and smaller until even 4-sides-glued watercolour pads are produced. All seconds (paper with imperfections) get fed back into the front-end for making new paper, and Paul was kind enough to give me some seconds which proves amazingly versatile watercolour, acrylics, and printmaking paper!
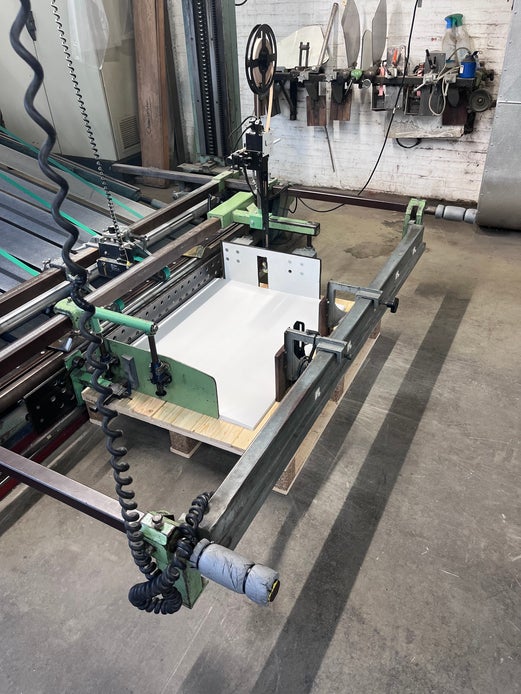
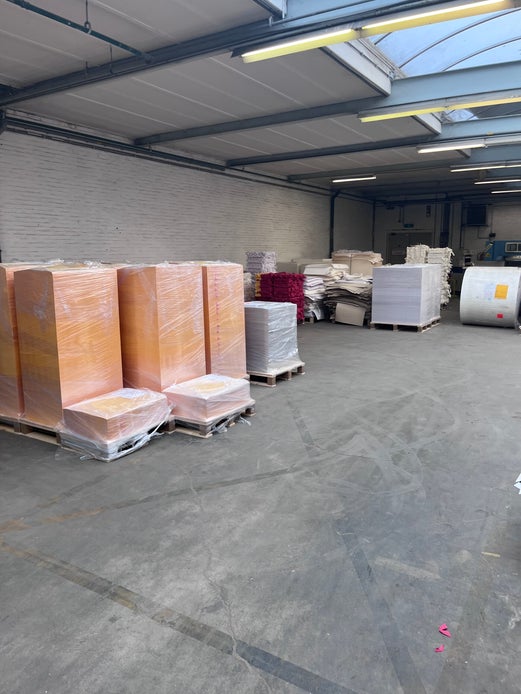
All in all it was a super informative morning and I would like to thank Paul for his time and the folk at the mill for their friendliness.
Add comment
Comments